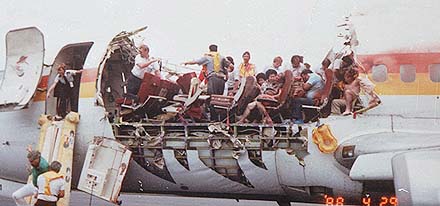 |
On April 28, 1988, an Aloha Airlines 737's fuselage blew open at 24,000 feet, killing a flight attendant and injuring eight people.
Associated Press library photo April 28, 1988
|
Graphic: A different theory of Aloha Flight 243
Studying what goes wrong is Austin's passion
Austin's Web site: www.disastercity.com
By Gary Stoller
USA Today
As an Aloha Airlines jet began landing on Maui, passenger Matt Austin noticed the luggage racks rattling and swaying when the thrust reversers came on.
It didnt startle him. He had seen that happen before on other older Aloha jets. But Austin remembered the name painted across the planes exterior: Queen Liliuokalani. It was a 19-year-old Boeing 737.
A week later on April 28, 1988 the same jets roof ripped open 24,000 feet over the Pacific Ocean, killing one flight attendant and seriously injuring seven passengers and a crew member. Austin counted himself lucky. Aloha Flight 243s last flight didnt really begin to grip him until the next year, when the National Transportation Safety Board issued its accident report.
This is a detective story. Its about a mystery that aviation professionals say was solved 12 years ago and the persistence of Austin, a former Hawaii boiler inspector, who has spent all those years and $45,000 of his money trying to prove that the experts got it wrong.
Its also about an accident that forever changed maintenance practices for old planes and about an alternative theory that could have far-reaching consequences. Finally, its about the intriguing possible parallels between boiler safety and airplane safety.
Austin, a mechanical engineer, has no professional expertise in airplane accidents. He is an expert on boilers; the NTSB once consulted him about a train boiler explosion in Gettysburg, Pa. Austin, 43, runs a consulting business, Hawaiian Steam Engineering, which designs, inspects and restores boilers and locomotives. He also consults for the Navy on servicing nuclear submarine power plant components.
Since 1989, Austin has researched the Aloha accident independently, always maintaining that his only motivation is "engineering truth" and a conviction that sharing his insights can prevent similar accidents. He has a Web site, www.disastercity.com, where he details his theories on the Aloha accident and other disasters.
If Austins theories are correct, a design that is intended to prevent catastrophic failures on nearly all Boeing jets could be flawed. It may even pose a danger to passengers, Austin says. Boeing says the design meets FAA requirements and works as intended.
Old planes called unsafe
Austin also says his study has convinced him that:
Old jets are not safe to fly, even if all required maintenance has been done.
The FAAs aging aircraft program, which requires airlines to inspect and repair old jets, should be scrapped. The program allows planes to fly beyond their design life and relies on airline inspectors who may not detect all structural problems, he says.
To reach those conclusions, Austin purchased and pored over more than 4,000 pages of NTSB accident findings. He attended a course for airline maintenance managers on aging aircraft and studied books for aeronautical engineers. He bought special computers to study the NTSBs photos of the accident and related forensic evidence.
Austin also corresponded with NTSB investigators, FAA officials and a Boeing engineer. The investigators stand by the NTSBs conclusions but say they respect Austins engineering knowledge.
"In every accident I ever worked, all kinds of crazies came out of the woodwork with theories about what happened," says former NTSB investigator Brian Richardson, who led the NTSB group that studied why the Aloha jet broke apart. "Matt Austin is not one of those people. He has good, solid credentials, and hes not going off the deep end."
The NTSB says it will not reopen the accident investigation, but Richardson says the FAA should study Austins theory. Then goes a major step further.
"Matt may well have nailed the cause of the accident," he says. "I dont really know."
Aloha Airlines no longer flies the 737-200 "basic" planes that were in use at the time of the accident. The carrier's current aircraft, 737-200 "advanced," are manufactured differently and are not related to that particular aircraft.
Aloha Flight 243 was bound from Hilo to Honolulu when its roof tore off. An emergency landing was made in Maui.
Many aviation experts consider the flight the most significant accident in commercial aviation. It showed how inadequate airline maintenance procedures and poor FAA oversight can result in tragedy, and it prompted an FAA program to more vigilantly inspect aging airplanes.
The NTSB, which investigated the Aloha accident, concluded the jets roof and walls tore off in flight because multiple fatigue cracks existed in the jets skin.
Those cracks developed, the NTSB said, because lap joints that were supposed to hold the fuselage together became corroded and failed. A lap joints connects two overlapping metal sheets of the fuselage.
The role of lap joints on the Aloha plane is what first captured Austins attention. He read a story about lap-joint failure in the accident and realized the same words had been written about a boiler explosion in Brockton, Mass., in 1905.
The danger of failed lap joints is well known in the boiler industry, which stopped using them on large boilers in the 1920s. In Brockton, a shoe factory boiler explosion collapsed a building, killing 58 people and injuring 117 others.
When a boilers lap joint fails, a hole opens in the boilers shell. The water inside instantly turns to steam, and increased pressure causes an explosion. Such a phenomenon is known as a fluid hammer, which Austin says caused the Aloha accident.
If Austins theory is correct, it solves a question that the accidents investigators asked: Why didnt Boeings "fail-safe" design, which is supposed to prevent a massive breakup, work?
Boeing says the 737 was designed to decompress safely with as much as a 40-inch crack in the planes skin, the 0.036-inch thick, aluminum outer layer of the fuselage. Instead of an explosive decompression, the hole in the skin is supposed to release internal pressure in a controlled way. In the Aloha accident, investigators concluded that more damage occurred about 18 feet of the fuselage tore away because many fatigue-caused cracks had gone undetected.
Austin says that a weakened fuselage was not the main reason for the extensive damage.
A 10-inch-by-10-inch hole opened, he says, in the roof of the cabin at a location known as body station 500. (Body stations are points on the fuselage that are measured in inches from near the nose of the jet to the rear.) A powerful stream of air swept an Aloha flight attendant off her feet and toward the hole, Austin says. Her head and right arm went through the hole, he says, but her body momentarily plugged it, blocking the escaping air and creating a jolt of pressure that ripped the jet apart. The flight attendant was swept out, and her body was never found.
"Slamming the door on a 700 mph jet stream creates a localized, short-duration high-pressure spike, up to several orders of magnitude (greater than) the allowable design pressure," Austin says. "This is a fluid hammer."
Forensic evidence, Austin says, shows where the flight attendants skull struck the exterior of the plane. The location of the skull print is consistent with the location of a plugged hole at body station 500, he says.
The NTSBs official accident report says, however, that the breakup of the jet began about 5 feet farther forward, at about body station 440.
But Richardson, the former NTSB investigator, says Austin pinpointed a mistake in the NTSBs report. He says he always assumed the breakup began close to the point that Austin says.
The wreckage that could reveal where the breakup occurred is at the bottom of the Pacific Ocean.
NTSB chief disagrees
USA Today brought Austins analysis to NTSB Chairman James Hall, who joined the board five years after the Aloha accident and recently announced his resignation. He said Austins theory makes sense, but the NTSB doesnt believe it happened that way.
"We dont disagree with Mr. Austins explanation about how an airplane can decompress at 24,000 feet after a 10-inch-by-10-inch hole is blown open in the skin and about how devastating the fluid hammer effect can be at this altitude," Hall said in a letter. "We disagree, however, with his conjecture involving the role the flight attendants body played.
"The roof of the Aloha airplane came off as a result of multiple site damage mainly, small fatigue cracks· These cracks joined together, resulting in the catastrophic separation of the skin."
Austin agrees that fatigue cracks weakened the structure, but he says the plane wouldnt have ripped apart had the hole not been plugged. And, Austin adds, "The NTSB validated my fluid-hammer theory. They couldnt say anything more without reconvening a pool of experts and reopening the investigation."
Richardson says he never heard of the fluid-hammer theory until Austin explained it. He says, though, hell stand behind his and the NTSBs conclusions. "We never thought that the hole in the fuselage remained small enough long enough for anything to plug it and produce the kind of pressure spike that is common to the pressure vessels that you are familiar with," Richardson wrote Austin.
Austin says, however, that the difference between the NTSBs findings and his analysis is, "Were 60 inches and probably 20 thousandths of a second apart."
He says he enlarged NTSB photos of the skull print, used a computer to view them from a different angle and pinpointed the skull prints exact location. "The skull print is the key," Austin says. "It wouldnt be there so graphically if the flight attendant didnt plug the hole. If there would have been an out-rush of air without a hole being plugged, her whole body would have been sucked out at once away from the aircraft."
Austin also corresponded with FAA officials in 1998. He was told that the FAA intended to do studies on his theory, but the agency later said it could not do the work because Congress had cut the FAAs research budget. King Frey, a retired aeronautical engineer who worked for two aircraft manufacturers, Hughes and Douglas, and for Northrop Grumman, which makes fuselages for 747s, buys the fluid-hammer theory.
"Matts reasoning and logic is right on target, and he has an excellent, probable theory that should be researched," Frey says. The odds are very small that such a phenomenon will occur, Frey says, "but rare things do happen."
As 737s get older, however, the theory raises the possibility from an astronomically small number to a number that should be taken seriously, Frey says. The increased possibility of a fluid-hammer effect, he says, needs to be heeded by Boeing and airline mechanics.
Fly it til it breaks
Regardless of whether hes right about the Aloha accident, he questions whether a plane can be designed for a safe decompression when a fuselage tears open. That would cause a powerful stream of air to escape from the cabin, he says, which could sweep up people or objects not belted down.
"Safe decompression is a fly-it-til-it-breaks philosophy," he says. "Its stupid to have a design concept that says a plane is OK until it blows a hole at 24,000 feet."
But Boeing officials say their design is sound and meets FAA regulations. Further, the company says, it tested the plane for the theory that Austin has. Boeings Jack McGuire says computer simulations were done in 1965 to test what would happen if a 40-inch hole one much larger than the hole that Austin believes popped open on the Aloha plane was plugged. The tests showed that cabin pressure is maintained longer, increasing passengers chances of survival, he says.
"I think its worth determining if this type of scenario should be a design consideration in the future," says Richardson, now an airline pilot. "Testing by the FAA/manufacturer is the only way to determine if it can happen in an aircraft."
FAA officials in Washington did not respond to written questions about safe-decompression design and aging aircraft.
Richardson and other aviation experts say the FAA should study the fluid-hammer phenomenon.
"The industry needs to be constantly reminded of the past so it can be ever vigilant in the future," he says.
Thats Austins credo. "Disasters keep recurring because we dont learn from those that have struck in the past," he says. "History is repeating itself before our eyes."
[back to top] |